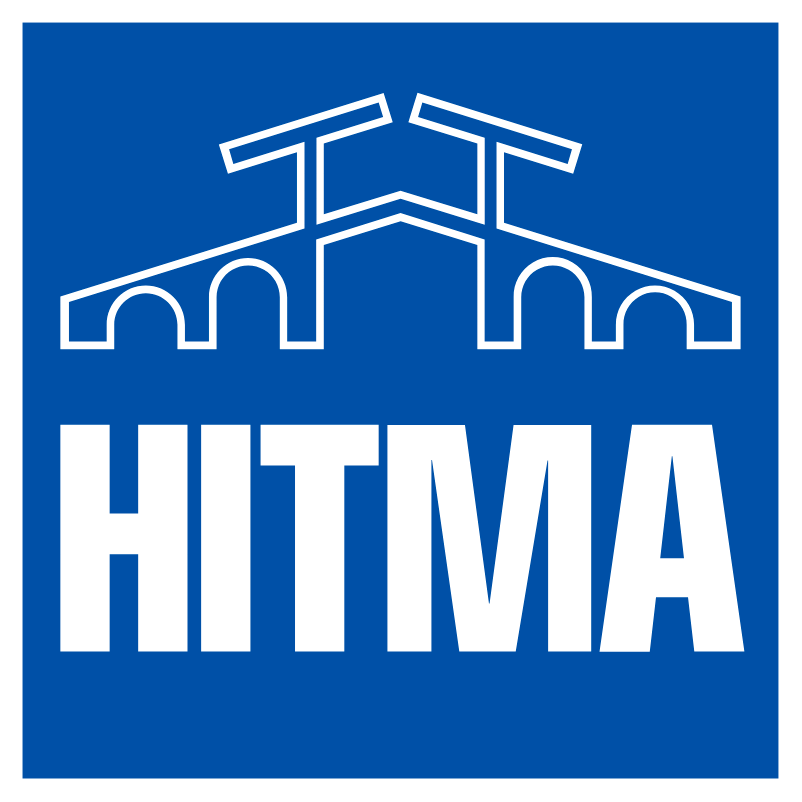
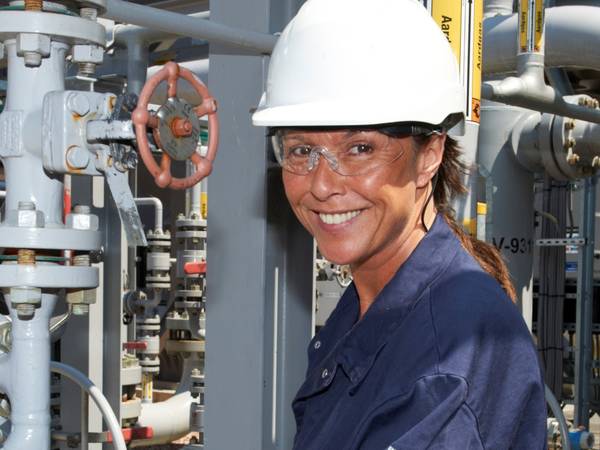
Van klanten die in de praktijk met veerveiligheden werken, krijg ik nog wel eens vragen over de invloed van tegendruk (back pressure) op veerveiligheden. In dit blog zal ik proberen hierover meer duidelijkheid te geven. Dat doe ik aan de hand van de resultaten van uitvoerige tests met veerveiligheden van verschillende fabrikanten door de Universiteit van Milaan.
Voordat ik de uitkomsten van het onderzoek behandel, geef ik eerst een korte omschrijving van de verschillende soorten druk (pressure) en veel gebruikte termen. Met vermelding dat de test zijn gedaan met een gasvormig medium (gas/vapour). Bij vloeistof (liquid) is dit weer een ander verhaal en zouden de uitkomsten anders zijn.
Optredende drukken met bijbehorende termen bij veerveiligheden
Pressure definitions
Tegendruk (back pressure)
Tegendruk is de druk aan de uitlaatzijde van een veerveiligheid (pressure relief device) als resultaat van de druk in een ontladingssysteem.
Back pressure
We maken onderscheid tussen 3 soorten tegendruk (back pressure):
Back pressure – superimposed constant
2. Back pressure – superimposed variable
3. Back pressure - built up
Superimposed of built up back pressure heeft een sterke invloed op het openen en de flowcapaciteit van veerveiligheidskleppen. Het is algemeen bekend dat deze functie verband houdt met een vermindering van de disc (klep)lift en/of met het ontstaan van een subsonische flow (stroom) door de klep.
Laboratoriumtests door universiteit van Milaan
Bij laboratoriumtests, uitgevoerd door de universiteit van Milaan op veerveiligheden van vijf verschillende merken, speciaal ontworpen om onder tegendruk te werken, kwam een verschil naar boven tussen de door de fabrikant gegarandeerde prestaties en de werkelijke klepprestaties. Dit verschil kan zo groot zijn dat de beschermde apparatuur boven de MAWP (maximum allowable working pressure ) ofwel de maximaal toelaatbare druk uitkomt.
De gecertificeerde afsteldrukken van de veerveiligheden, bij gebruik onder atmosferische tegendrukomstandigheden, kwamen wel in buurt, maar er was een aanzienlijk verschil wanneer de tegendruk werd verhoogd ten opzichte van de atmosferische waarde. Dit was met name het geval wanneer de tegendrukverhouding (verhouding tussen de absolute tegendruk en de ontlastdruk) werd verhoogd met 25%. De toepassing van een bellow of balg kan hierbij helpen, maar het probleem niet oplossen.
Onderzoek werking afsluiters onder verschillende omstandigheden
De ervaring die door de universiteit in Milaan is opgedaan in het laboratorium voor onderzoek, ontwikkeling en certificering van afsluiters heeft een producent van veerveiligheden ertoe gebracht het gedrag van afsluiters binnen vijf verschillende applicaties te testen. De geteste kleppen werden besteld met dezelfde technische specificaties, inclusief de eis om onder tegendruk te kunnen werken.
|
Results of atmospheric back-pressure tests |
|
||
Valve |
A B |
C |
D |
E |
Blow down % |
37 % 7.3 % |
6.7 % |
5.6 % |
5.33 |
K/Knom At 10% over pressure. Table 2. Summary of atmospheric |
1.02 1.0
back-pressure test results |
0.95 |
1.01 |
0.95 |
Resultaten van tests bij atmosferische tegendruk
Hier volgen de belangrijkste resultaten van de tests die zijn uitgevoerd onder atmosferische tegendrukomstandigheden voor de vier veiligheidskleppen. K is de werkelijke afvoercoëfficiënt, terwijl K-nom door de fabrikant is opgegeven bij atmosferisch tegendruk.
Het meest opvallende kenmerk is de bijzonder hoge afblaaswaarde van klep A. Deze is bijna 5 keer zo hoog is als door de fabrikant is aangegeven. De rest van de gegevens is redelijk in overeenstemming met de opgegeven waardes.
Resultaten tests met tegendruk ( built–up)
In figuur 1 zie je de resultaten van de tests die zijn uitgevoerd op de vijf kleppen. De grafieken tonen een vermindering van zowel de door de fabrikant opgegeven (de stippellijn) als de feitelijk gemeten (de ononderbroken lijn) afvoercoëfficiënt versus de tegendrukverhouding.
De verhouding K / Knom vertegenwoordigt de verhouding tussen de feitelijk gemeten ontladingscoëfficiënt bij een bepaalde tegendrukverhouding en de afvoercoëfficiënt zoals opgegeven door de fabrikant voor dezelfde klep die werkt onder atmosferische tegendruk.
Resultaten tonen aan dat de verwachte afname van de stroomsnelheid van kleppen B en C en E sterk wordt onderschat. Bovendien wordt een zeer verrassend resultaat gevonden voor klep E. Deze klep vertoont een dramatische afname van de stroomcapaciteit wanneer de tegendruk de 18% bereikt. Er werden geen verdere tests uitgevoerd op dit apparaat, omdat de balg (bellow) brak toen de klep werd bediend tijdens de eerste test bij superdruk.
Volgens het rapport van de onderzoekers functioneerde de balg correct toen de opgebouwde back-pressure-test werd uitgevoerd, maar deze hypothese kan niet worden bevestigd. Dit ongeval onderstreept echter het belang van de betrouwbaarheid van de balg en ondersteunt de regelgeving: “In het geval van een falen van een balg bellow, zal de veiligheidsklep bij openen zijn gecertificeerde capaciteit niet meer dan 1.1. maal met de maximaal toelaatbare druk (design pressure) van de te beschermen apparatuur overschrijden.”
Bij klep A zien we dat de afnametrend van de capaciteit door de fabrikant is voorzien en dat de vermindering van de stroomcapaciteit vrij laag is. Hierbij wordt opgemerkt dat bij een tegendrukverhouding van 68% de afblaascoëfficiënt (coëfficiënt of discharge) een reductie van slechts 20% heeft ondergaan. Aan de andere kant vertoont de klep grote problemen bij het sluiten (reseating). Dit was eerder ook geconstateerd in de atmosferische tegendruktests en zal ook worden opgemerkt bij de supersonic-tegendruktests.
De fabrikant van klep B verklaart dat de discharge-coëfficiënt niet gevoelig is voor tegendruk, totdat deze 50% bereikt, waarbij een verlaging van 3% van K wordt verwacht. Maar geheel tegenstrijdig hieraan, tonen de experimentele resultaten aan dat de ontladingscoëfficiënt in een progressieve lineaire lijn loopt, beginnend bij een tegendrukverhouding van 20% tot 48%, waarbij de ontladingscoëfficiënt ongeveer 2/3 is van die van de atmosferische druk. Bovendien vertoont de klep bij dezelfde opgebouwde tegendrukverhouding een duidelijke instabiliteit en heeft de disc/klep de neiging om te sluiten.
De uitkomsten van deze tests onderstrepen de behoefte aan een goed gedefinieerde testprocedure voor de evaluatie van het gedrag van veiligheidskleppen die onder tegendruk werken.
Wat klep C betreft, verklaart de fabrikant dat de opgebouwde tegendruk de capaciteit niet beïnvloedt. Uit de grafiek blijkt duidelijk dat dit niet klopt met het daadwerkelijke liftgedrag van de veerveiligheid. De metingen laten een dramatische vermindering van de flowcapaciteit zien. Al bij een tegendruk van minder dan 30% (K / K-nom = 0,63). Door de tegendruk te verhogen, loopt de afvoercoëfficiënt (discharge coëfficiënt) terug tot een minimumwaarde van 43% van de nominale waarde.
De fabrikant van klep D geeft aan dat er geen verlaging van de afvoercoëfficiënt wordt verwacht voor de tegendruk (back pressure) binnen 25%, terwijl metingen een verlaging van K / K-nom tot 0,95 laten zien. De stromingscapaciteit vermindert tot 80% van de nominale snelheid voor een tegendrukverhouding van 34%, waarna de veerveiligheid snel sluit (re -seated).
Resultaten superimposed back pressure-tests
Tests onder ‘superimposed back pressure’ (tegendruk) hebben als doel de functionele en stroomcapaciteitseigenschappen van veiligheidskleppen binnen een limietoverdruk van 10% te verifiëren, geëvalueerd op basis van de ingestelde druk gemeten in atmosferische tegendruktests.
Klep A is getest bij drie verschillende tegendrukwaarden tot een tegendrukverhouding van 65%. Alle tests tonen dezelfde kenmerken. De klep knalt voor de overdruk van 10% en de afvoercoëfficiënt bereikt dezelfde waarde, gemeten in de opgebouwde tegendruktesten voor dezelfde tegendruk- verhouding.
Zoals eerder vermeld, wordt dit duidelijk voorspelde gedrag gevolgd door een vrij hoge blow down. In het bijzonder wordt de blow down verminderd ten opzichte van de atmosferische tests (37% in tab. 1) en blijft afnemen met de toenemende tegendruk: oplopend van een tegendrukverhouding van 40% tot 65% vermindert de blow down van 16,5 % tot 12%, in ieder geval boven de door de fabrikant opgegeven limiet van 7%.
Klep B opent “pop-up” voor de overdruk van 10% is bereikt, maar alleen bij een tegendruk van minder dan 33%. Voor hogere tegendruk is pas een pop-up bij een overdruk die oploopt tot 13% bij 37% tegendruk, hetgeen overeenkomt met de limiet aangegeven in de technische specificatie. Zodra de klep is geopend, bereikt de afvoercoëfficiënt dezelfde waarden als gemeten in de built up tegendruktests. Natuurlijk is de stroomcapaciteit zeer laag wanneer de veerveiligheid niet opent. De blowdown blijft altijd binnen de aangegeven limieten.
Klep C opent binnen de 10% overdruk en sluit binnen de aangegeven limiet. De coëfficiënt of discharge bereikt altijd dezelfde waarden zoals gemeten in de built up tegendruktests. Wel zijn de flow –rates erg klein in vergelijking met de opgegeven waarden (zie klep C in fig. 1). ,
Klep D opent binnen 10% overdruk alleen voor een back pressure van minder dan 25%, zoals gespecificeerd door de fabrikant.
Boven de 25% vereist de opening van de klep een over pressure van 16% voor een back pressure van 30%. De blow down is zoals opgegeven door de fabrikant en de coëfficiënt of discharge komt overeen met de waarde zoals vastgelegd in de built up back pressure-tests.
Conclusies onderzoek
Wat kunnen we concluderen uit de resultaten van deze operationele en flowtests uitgevoerd op vijf commerciële veiligheidskleppen die zijn geleverd volgens dezelfde technische specificaties, zoals besproken en gedocumenteerd? Nadat de klepprestaties zijn vergeleken met de informatie van de fabrikant, viel het volgende op:
- Atmosferische Back Pressure druk testen tonen redelijk goede overeenstemming met de verklaring van de fabrikant voor vier van de vijf afsluiters, terwijl slechts één monster een blow down van 37% vertoont in plaats van de aangegeven 10%.
- Super imposed en built –up druk testen laten meerdere afwijkingen zien met de opgegeven waardes van de fabrikant, zowel wat betreft de werking als de flow door de kelp.
- Bij één van de vijf ging de Bellow (balg) kapot bij het begin van de tegendruktests. Dit geeft aan dat het heel goed mogelijk is dat er in de praktijk op locatie, wanneer het nodig is dat de klep opent onder (Back Pressure) tegendrukomstandigheden, de procesapparatuur kan worden blootgesteld aan een druk hoger dan 1,1 maal de maximaal toelaatbare druk. Dit kan te wijten zijn aan het onvermogen van de klep om binnen de overdruklimiet te openen en/of aan de vermindering van de flow capacity/stromingscapaciteit veroorzaakt door een slechte disc lift en/of het ontstaan van een subsonisch regime, ook wanneer de rug- drukverhouding is lager dan het kritische niveau (0,528).
Noodzaak gedefinieerde testprocedure
De uitkomsten van deze tests onderstrepen de behoefte aan een goed gedefinieerde testprocedure voor de evaluatie van het gedrag van veiligheidskleppen die onder tegendruk werken. Het is lastig om een complete range te testen die moet voldoen aan de limieten van de testopstelling. Laboratoriumtests die zijn uitgevoerd op veiligheidsklepmodellen tonen aan dat de afmetingen en de verhouding van de valve body, van de uitlaat tot het doorlaatoppervlak (nozzle area), de flowcapaciteit binnen hetzelfde groottebereik sterk beïnvloeden.
Het is dus alleen mogelijk om met uitgebreide laboratoriumtests de prestaties van een volledig range veerveiligheden onder back pressure (tegendruk) redelijk te meten. Maar deze tests zijn wel zeer belangrijk. Ze zullen weer leiden tot betere drukapparatuur én meer veiligheid voor de eindgebruikers.